2024 Forfatter: Howard Calhoun | [email protected]. Sidst ændret: 2023-12-17 10:22
Forsinkede forkoksningsenheder er den mest almindelige hardwareløsning til sværolieraffinering. Deres enhed inkluderer 2 hovedmoduler - reaktor, hvor råmaterialet opvarmes og koks, og mekanisk behandling. Designet af anlæg udføres i etaper og omfatter beregning og valg af procesudstyr, fastlæggelse af tekniske og økonomiske indikatorer.
Destination
Teknologisk forkoksningsproces er en af måderne til olieraffinering. Dens hovedformål er at opnå store klumpede petroleumskoks. Der bruges 3 koksningsmetoder i industrien:
- Periodisk, i terninger. Råmaterialet fyldes i et vandret apparat, opvarmes med en brændkammer nedenunder og brændes derefter i 2-3 timer. Derefter afkøles ovnen, og det færdige produkt aflæses. Denne metode er den enkleste og mindst produktive.
- Kontinuerlig. Denne metode er stadig på stadiet af industriel udvikling.
- Semi-kontinuerlig, modtaget i øjeblikketden mest udbredte.
Ultra-forsinkede forkoksningsenheder er den nyeste type procesudstyr. I dem forvarmes råmaterialet i en ovn og overføres derefter til uopvarmede reaktionskamre, som har et termisk isoleringslag for at opretholde den nødvendige temperatur. Antallet og størrelsen af reaktorer, kraften af ovne påvirker hele anlæggets ydeevne.
Driften af den første DCU i Rusland blev startet i 1965 på Ufaneftekhim. Anlæggets forsinkede koksanlæg er stadig i drift i dag. Efter genopbygning i 2007 er dens produktivitet omkring 700-750 tusinde tons/år i form af massen af forarbejdede råmaterialer.
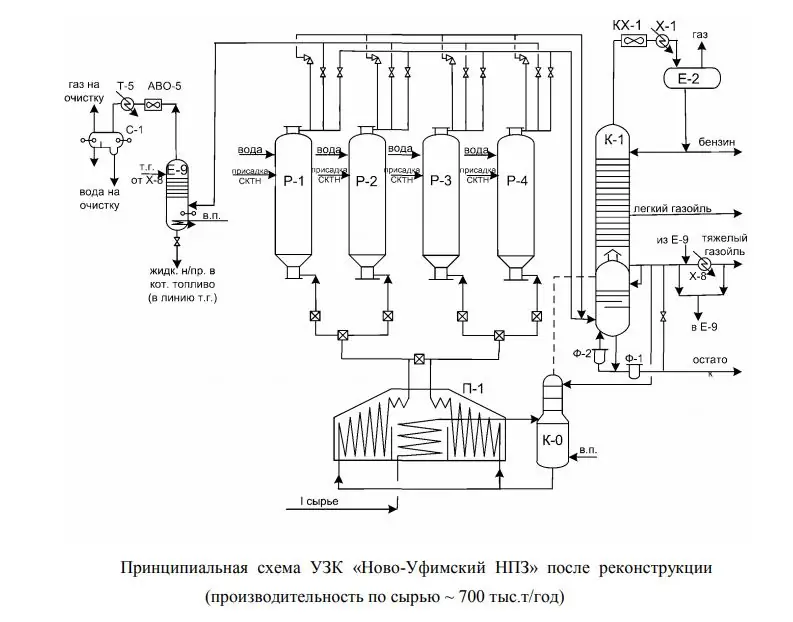
Slutlige produkter
Følgende stoffer opnås ved ultralydstestning, undtagen koks:
- koksgasser (bruges som procesbrændstof eller behandles for at opnå propan-butanfraktion);
- benzin;
- koksdestillater (brændstof, råmateriale til krakning).
På indenlandske ultralydstestmaskiner er koksudbyttet 20-30 vægtprocent. Denne indikator afhænger primært af kvaliteten af råvarer. Den metallurgiske industri oplever det største behov for dette produkt (produktion af anoder og elektroder, aluminium, slibemidler, carbider, carbon-grafitmaterialer, ferrolegeringer). Ud over den første Ufa DCU er der også bygget andre forsinkede coker-enheder i Rusland: på Omsk Refinery, Novokuibyshevsk Refinery, LLC LUKOIL-Volgogradneftepererabotka, LUKOIL-Permnefteorgsintez, LUKOIL-Permnefteorgsintez, hos Angarsk Petrochemical Company, NOVOIL OJSC (Ufa), TANECO PJSC (Nizhnekamsk).
Råvarer
Fødevarematerialer til koksning er opdelt i 2 grupper: produkter fra primær og sekundær forarbejdning. Følgende stoffer anvendes som råvarer i forsinkede koksningsenheder:
- fuel oil;
- halvtjære;
- tar;
- kultjærebeg;
- asf alt og andre industrielle olieprodukter;
- flydende kulrest;
- tung pyrolyse og skifertjære;
- termiske revnedannelsesrester;
- råoliebitumen og tunge olier.
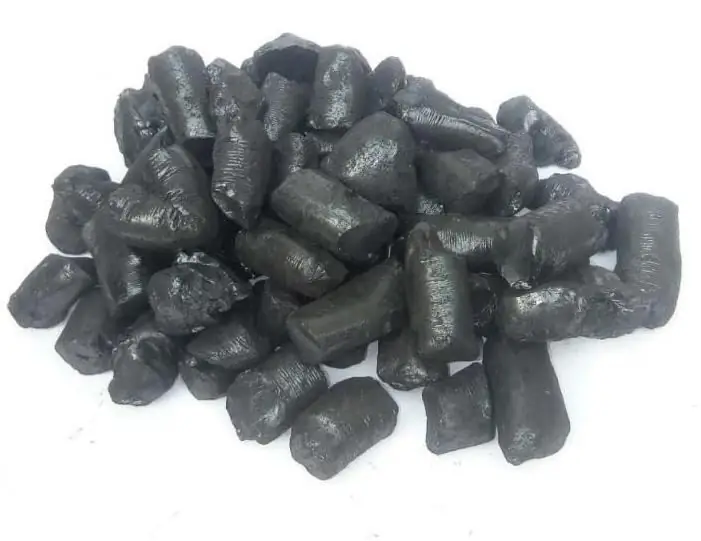
Stærkt aromatiserede olierester er det mest almindelige råmateriale i øjeblikket.
Indflydelse på teknologiske parametre
Følgende parametre for koksværket afhænger af fodermidlernes egenskaber:
- effektivitet af reaktionskammeret;
- kvalitet af modtagne produkter;
- koksudsalg;
- betingelser for processen.
De vigtigste råvareparametre er:
- Koksning, afhængig af indholdet af asf altharpiksholdige stoffer. Forkoksningsværdien bør være i området 10-20%. Med en mindre værdi falder koksudbyttet, og med en større ophobes aflejringer inde i spolerne i ovnene. Forkoksningskapaciteten bestemmes af massen af den faste rest i diglen efter opvarmning af olieproduktprøven i den.
- Density.
- Kemisk sammensætning. Fraskadelige urenheder, der har den største indvirkning på kvaliteten af koks, udleder svovl (det bør ikke være mere end 1,5 vægtprocent). Afhængigt af formålet med koks i den teknologiske proces er det at foretrække at bruge forskellige typer råmaterialer. Så for at opnå en fibrøs struktur af slutproduktet anvendes materialer med en paraffinbase.
Koksudbyttet er proportion alt med foderets tæthed og asf altenindhold.
Kokningsstadier
Den teknologiske proces i forsinkede koksanlæg er lang og kontinuerlig, fra levering af råvarer til aflæsning af det færdige produkt. Konventionelt er det opdelt i 3 faser:
- Dekomponeringsreaktioner, dannelse af destillatfraktioner, mellemprodukter, kondensation.
- Væsentlig reduktion i indholdet af umættede kulbrinter i gasser, en stigning i molekylvægten af restkomponenterne, ringslutningsreaktioner.
- Forøgelse af indholdet af asf altener i restproduktet op til 26%, reduktion i mængden af harpiks og olier. Konverter flydende rest til fast koks.
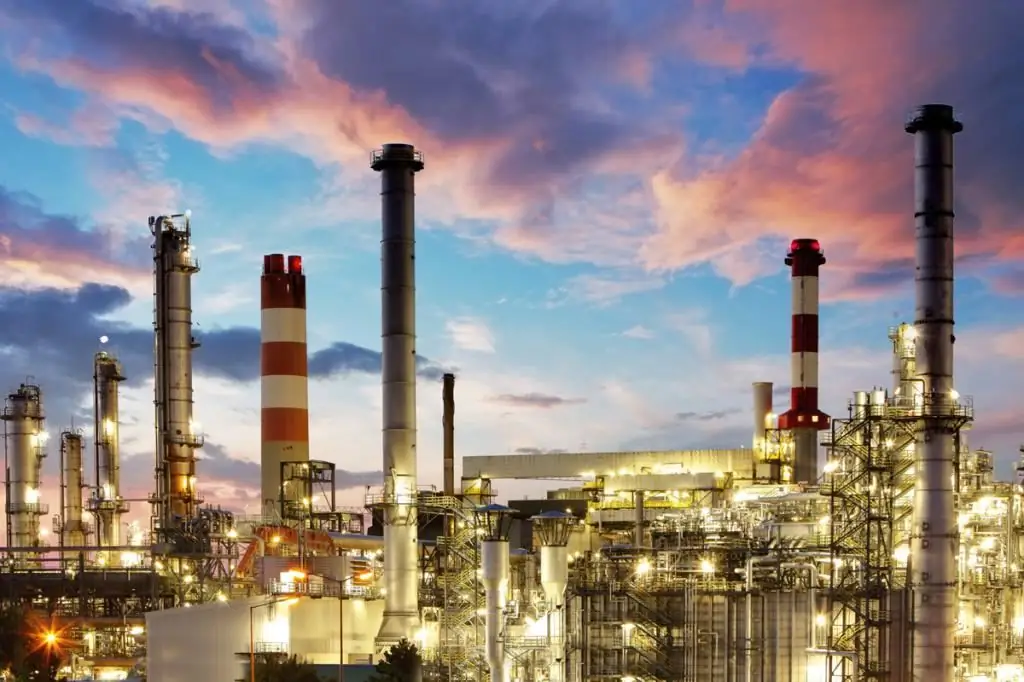
Klassificering
Der er 2 hovedtyper af forsinkede koksningsenheder i henhold til deres layout: enkeltblok og dobbeltblok.
Blandt to-blok-anlæg er der 4 typer, som er kendetegnet ved følgende design og teknologiske funktioner:
- Indvendig diameter af koksingskamre – 4,6 m. Teltvarmeovne, fire kamre, der fungerer i par. Petroleum og gasolie opnået under forkoksningsprocessen bruges til opvarmning.
- Colakamre Ø 5,5 m. Råmateriale - straight-run brændselsolier med introduktion af stærkt aromatiske kulbrinter, som øger udbyttet af et kvalitetsprodukt.
- Reaktorer lavet af legeret stål Ø 5,5 m, højde 27,6 m, rørformede ovne med volumetrisk lægningsbrænder, overliggende ventiler med øget tværsnit, radioaktive niveaumålere, der gør det muligt at registrere placeringen af koks-skum faseadskillelsen. Den seneste innovation hjælper med at udnytte reaktorens nyttige volumen bedre. Levering af turbulatorer med rensemiddeltilsætningsstoffer for at reducere forkoksning af spoler, afkølet gasolie i hovedrør.
- Reaktionskamre Ø 7 m, højde 29,3 m. Aksial tilførsel af råmateriale til reaktorerne, hydraulisk system til udledning af koks med fjernbetjening, elektriske kraner, lagerbygninger med gulvtypelager.
Anvendt udstyr
Udstyr, som er udstyret med installationer af denne type, er opdelt i følgende grupper afhængigt af formålet:
- Teknologisk, direkte involveret i forkoksningsprocessen (ovne, kolonneudstyr, varmevekslere, reaktorkamre, terninger, køleskabe, pumper, rørledninger, instrumentering, haner og andre afspærrings- og koblingsventiler).
- Wastewater - opsamling og behandling af vand for at vende tilbage til arbejdscyklussen (afkøling og koksudvinding).
- Udstyr til aflæsning af koks fra kamre (terninger). I moderne mekaniserede installationer kan det være af en mekanisk og hydraulisk type (slynger, spil, kamme, kuttere, stænger, tårne, gummimanchetter).
- Enheder til transport og forarbejdning af det færdige produkt (modtagelse af slisker og ramper, kraner, transportører, feedere, knusere, lagre).
- Maskiner og udstyr til mekanisering af arbejde.
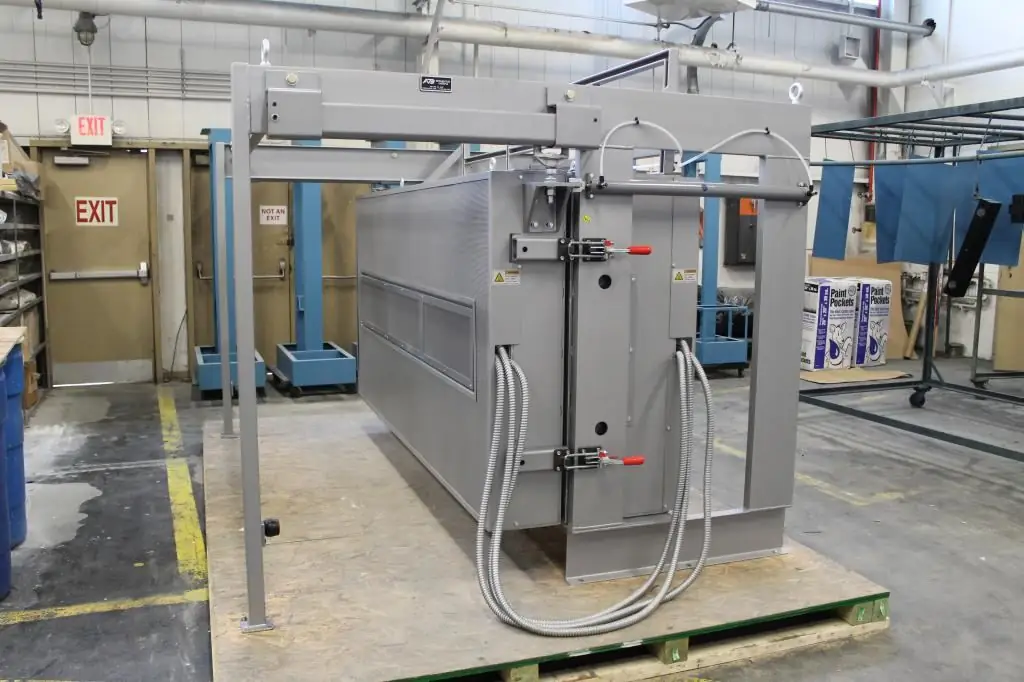
Når man designer forsinkede koksanlæg, er det nødvendigt nøje at overveje designet af reaktionskamre og ovne, da varigheden af arbejdscyklussen afhænger af pålideligheden af deres drift.
Procesparametre
De vigtigste parametre for koksteknologi er:
- Recirkulationsforhold, defineret som forholdet mellem den samlede belastning af ovnenes reaktionsspoler og belastningen af hele anlægget i form af råmaterialer. Med en stigning i værdien stiger udbyttet af højkvalitets koks, gas og benzin, men mængden af tung dieselolie falder.
- Tryk i reaktionskammeret. Dets fald fører til en stigning i udbyttet af gasolie, et fald i udbyttet af koks og gas og en stigning i skumdannelse.
- Procestemperatur. Jo større den er, jo højere er kvaliteten af koks med hensyn til mængden af flygtige stoffer, dens styrke og densitet. Den maksimale værdi er begrænset af risikoen for forkoksning af ovnen og rørledningerne, hvilket reducerer spolernes holdbarhed. Hver type råmateriale har sin egen optimale temperatur.
Opførelsen af forsinkede koksanlæg er forbundet med høje kapitalomkostninger. Derfor udføres oftest rekonstruktionen af et allerede fungerende kompleks af udstyr. Dette opnås ved at reducere cyklussenforkoksning, indførelse af nye reaktionskamre eller reduktion af recirkulationsforholdet.
Driftsprincip
Forsinkede koksningsenheder består af en eller flere parrede grupper af kamre, hvor det ene kammer fungerer på stadiet af koksproduktion, og det andet ved aflæsning eller i en mellemtilstand. Processen med nedbrydning af kildematerialet begynder i en rørovn, hvor det opvarmes til 470-510 °C. Herefter kommer råvaren ind i uopvarmede kamre, hvor den er dybt kokseret på grund af den varme, der fulgte med.
Gasformige og flydende kulbrinter udledes til fraktioneret adskillelse i en destillationskolonne. Koks kommer ind i den mekaniske forarbejdningsafdeling, hvor den losses, sorteres og transporteres. En brønd bores i laget af det færdige produkt, og en hydraulisk skærer er placeret i den. Dens dyser fungerer under tryk op til 20 MPa. Stykker af adskilt koks falder ned på en drænplatform, hvor vandet drænes. Produktet knuses derefter i mindre stykker og separeres i fraktioner. Dernæst flyttes koksen til lageret.
Principdiagrammet for ultralyden er vist i nedenstående figur.
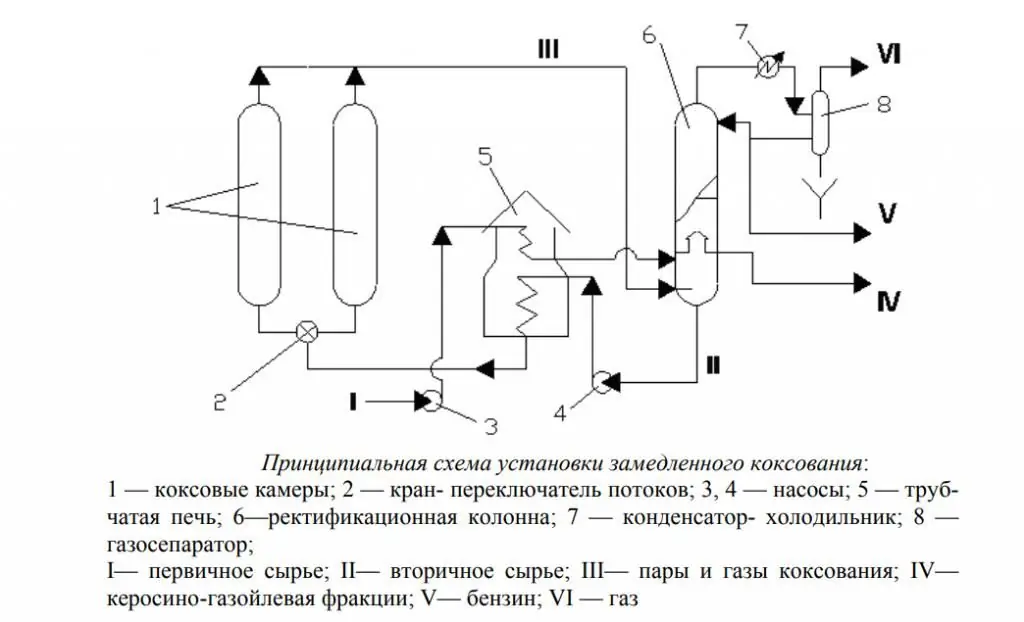
Coke-kamre
Kamrene er en reaktor, som er grundlaget for hele installationen. Driftscyklussen af kammeret er norm alt 48 timer, men i de senere år er ultralydsenheder, der fungerer i 18- og 36-timers tilstande, blevet designet.
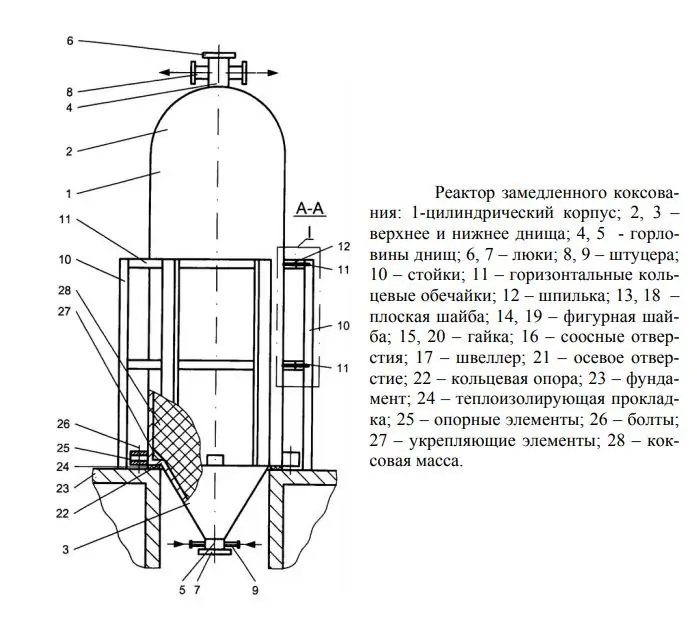
En reaktordriftscyklus består af følgende operationer:
- pålæsning af råvarer, koksproces (1 dag);
- fra (1/2 time);
- hydrotermisk behandling (2,5 timer);
- vandkøling af produktet, vandfjernelse (4 timer);
- aflæs produkt (5 timer);
- tætning af mandehuller, trykprøvning med varm damp (2 timer);
- opvarmning med oliedampe, skift til arbejdscyklus (3 timer).
Design
Det forsinkede koksningsenhedsprojekt udvikles i følgende rækkefølge:
- bestemmelse af den krævede produktivitet, t/år;
- ressourcebaseanalyse;
- udarbejdelse af en teoretisk materialebalance for koksningsprocessen for forskellige typer råmaterialer;
- bestemmelse af de vigtigste materialestrømme;
- udvikling af installationskonceptet;
- begrundelse for størrelsen og antallet af reaktorer;
- bestemmelse af varigheden af at fylde et kammer med koks og dets hydrauliske beregning, udarbejdelse af en tidsplan for driften af reaktoren;
- beregninger af temperaturbelastningen på kammeret;
- beregning af konvektions- og strålingskamre;
- udvikling af produktionslinjelayout;
- teknologiske beregninger af andet hovedudstyr (destillationskolonne, ovne, køleskabe osv.);
- udvikling af et overvågnings- og kontrolsystem, valg af automatiseringsværktøjer;
- beskrivelse af nødbeskyttelsesordninger;
- udvikling af miljøaspekter og sikkerhedsforanst altninger;
- fastsættelse af økonomiske indikatorer (kapitalomkostninger, antal servicepersonale, løn,produktionsomkostninger for råvarer og hjælpematerialer, årlig økonomisk effekt, produktomkostninger).
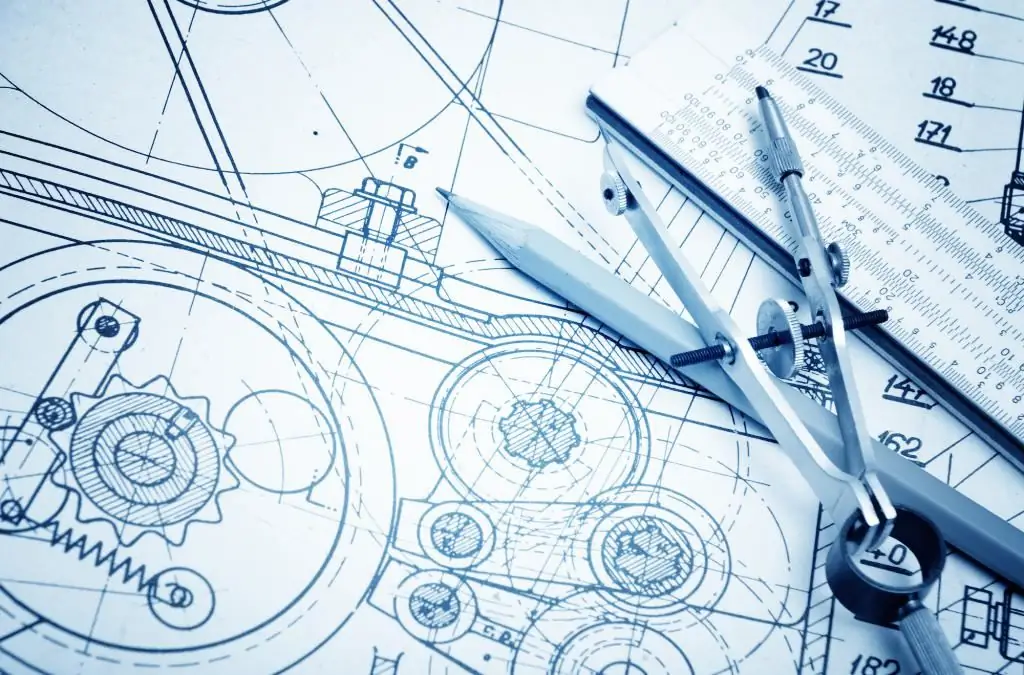
Beregning af kapaciteten af den forsinkede koksningsenhed på årsbasis foretages efter formlen:
N=P x t, hvor P er anlæggets kapacitet, t/dag;
t er antallet af arbejdsdage i et år.
Produktoutput i fysiske termer i henhold til basis- og designmulighederne bestemmes ud fra installationens materialebalance.
Anbefalede:
Stålsmeltning: teknologi, metoder, råmaterialer
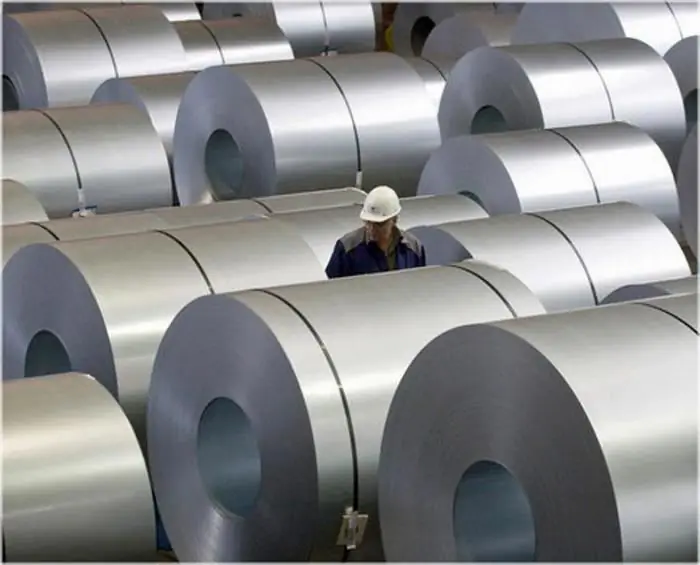
Jernmalm opnås på sædvanlig måde: åben eller underjordisk minedrift og efterfølgende transport til indledende klargøring, hvor materialet knuses, vaskes og forarbejdes
Trefaset netværk: effektberegning, tilslutningsdiagram
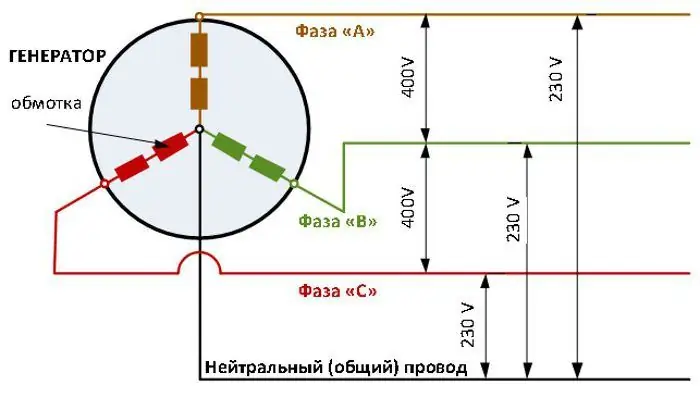
Når det er designet og vedligeholdt korrekt, er et trefaset netværk ideelt til et privat hjem. Det giver dig mulighed for jævnt at fordele belastningen på tværs af faserne og tilslutte yderligere strømforbrugere, hvis ledningssektionen tillader
Hvad er stof lavet af? Klassificering af stoffer efter type af råmaterialer, egenskaber og formål
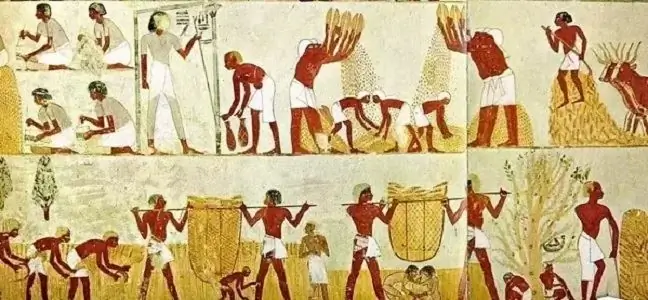
Når man bruger stof i hverdagen, har man ikke engang tanker om, hvor betydningsfuld denne opfindelse var for menneskeheden. Men uden stoffer ville livet være ubehageligt og utænkeligt! En person er omgivet af væv i alle sine livsaktiviteter. Hvornår dukkede det første stof op, og hvad er det nu lavet af? Lad os tale om det i artiklen
Produktion af polyurethanskum: teknologi, råmaterialer, udstyr
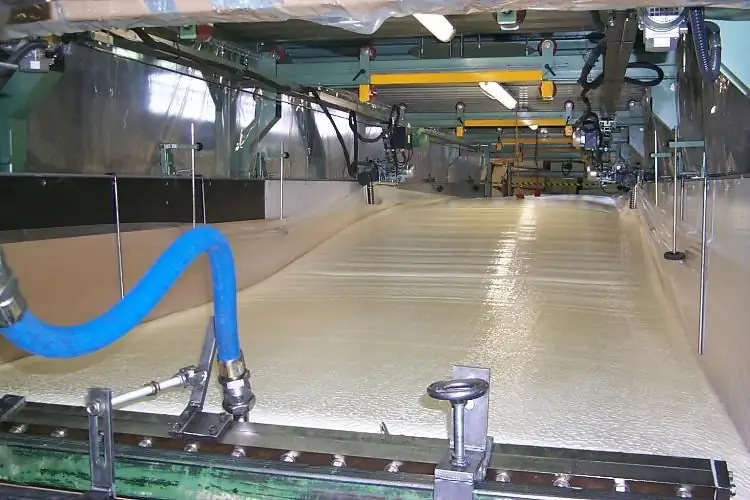
Montering af skum fra de sædvanlige metoder til tætning af vinduesåbninger er for længst gået over i status som et fuldgyldigt byggemateriale, som er meget udbredt i en række forskellige typer arbejde. De mange forskellige anvendelser af dette produkt bestemmer også behovet for en differentieret tilgang til teknologierne for dets fremstilling. Forskellene i produktionsmetoderne for polyurethanskum er dog mere af kosmetisk karakter uden at påvirke de grundlæggende teknologiske processer
PVC-rørproduktion: teknologi, råmaterialer og udstyr
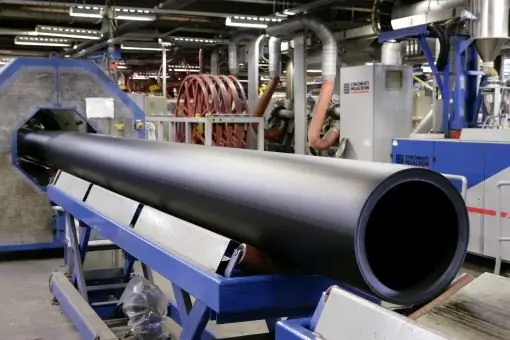
Rørformede produkter baseret på polyvinylchlorid (PVC) er meget udbredt i dag i en række forskellige områder og industrier fra den private sektor til store olie- og gasvirksomheder. Men processen med deres konsolidering på markedet var gradvis, da polymermaterialets fysiske og tekniske egenskaber er ringere end traditionelle metalmodstykker i en række kriterier. Men den moderne produktion af PVC-rør har på grund af indførelsen af avancerede teknologier øget produkternes ydeevne betydeligt