2024 Forfatter: Howard Calhoun | [email protected]. Sidst ændret: 2023-12-17 10:22
Kvaliteten af svejsningen bestemmes ikke kun af mesterens evne til at organisere lysbuen korrekt, men også af den særlige beskyttelse af arbejdsområdet mod ydre påvirkninger. Hovedfjenden på vejen til at skabe en stærk og holdbar metalforbindelse er det naturlige luftmiljø. Sømisolering fra ilt giver flux til svejsning, men ikke kun dette er dens opgave. Forskellige konfigurationer af sammensætningen af dette additiv med en kombination af beskyttende gasmiljø giver dig mulighed for at kontrollere parametrene for sømfugen på forskellige måder.
Flux-opgave
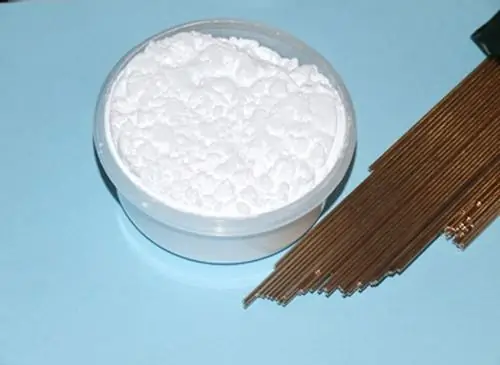
Svejsetilsatsen af denne type sendes til forbrændingszonen og har, afhængigt af smeltens karakteristika, en beskyttende og modificerende effekt på svejsedannelsesområdet. Materialet kan især udføre følgende funktioner:
- Oprettelse af slagge- og gasisolering til svejsebadet.
- Giver en svejset samlingvisse tekniske og fysiske egenskaber.
- Opretholdelse af lysbuestabilitet.
- Overførsel af elektrodemetal (eller trådsmeltning) til svejsezonen.
- Fjernelse af uønskede urenheder i slaggelaget.
Hvis vi taler om kompatibiliteten af forskellige flusmidler til svejsning med metaller, så har de mest almindelige mærker følgende formål:
- FC-9 – kulstoflegeringer i lavt legeret stål.
- AN-18 - højlegerede stållegeringer.
- AN-47 - lav- og mellemlegeret stål, kendetegnet ved højstyrkeegenskaber.
- AN-60 - lavlegeret stål, der bruges i rørledninger.
- ФЦ-7 - bruges ved svejsning af blødt stål ved høj strøm.
- FC-17 – højtemperatur fladecentreret strygejern.
- FC-19 - legeringer med et højt kromindhold.
- ФЦ-22 – bruges til at lave en filetsømsamling i arbejde med legeret kulstofstål.
- 48-OF-6 - bruges i svejseteknikker med tilslutning af højlegeret elektrodetråd.
Flux-kompositioner
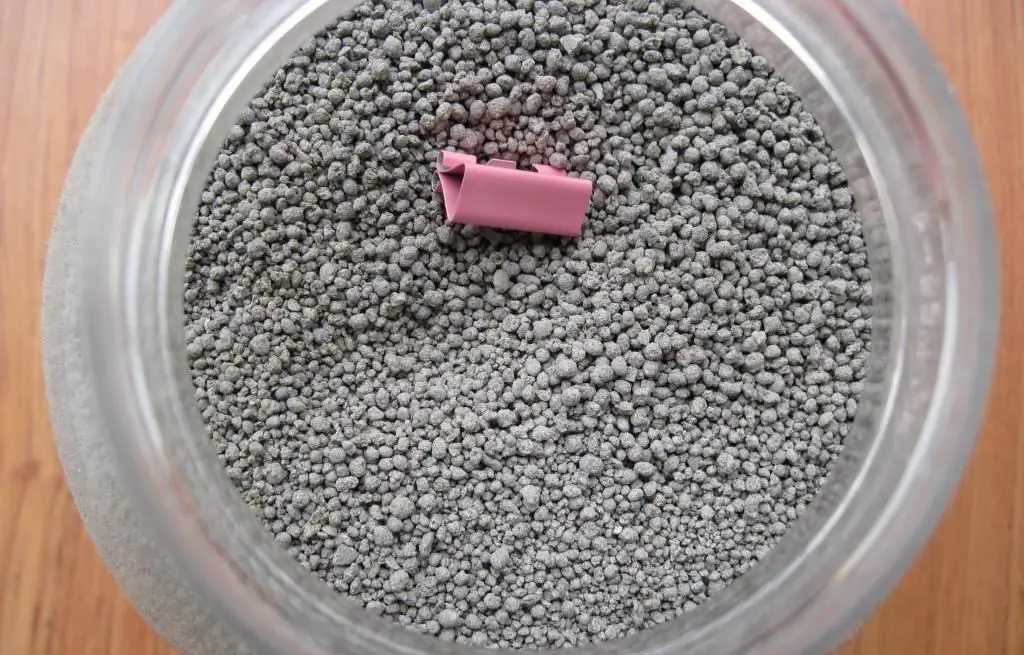
Fluxen i sig selv fremstilles som regel i form af et granulært pulver med en brøkdel af størrelsesordenen 0,2-4 mm. Men indholdet og oprindelsen af dette produkt kan være meget forskelligt og ikke altid ensartet. I denne henseende skelnes der mellem følgende typer flux til svejsning:
- Oxid. Det meste af indholdet er metaloxider og omkring 10 %står for andelen af fluorelementer. Denne flux bruges til at arbejde med lavlegerede og fluorstållegeringer. Afhængigt af indholdet opdeles oxidfluxsammensætninger også i siliciumfrit, lavt silicium og højt silicium.
- S altoxid. Sådanne pulvere kaldes også blandede, da fyldningen ligeligt kan dannes af oxider og s altforbindelser. Denne flussmiddel bruges til at behandle legeret stål.
- Saline. Tilstedeværelsen af oxider er fuldstændig udelukket, og fluorider og chlorider danner grundlaget for sammensætningen. Formålet med s altflux er elektroslaggomsmeltning og svejsning af aktive metaller.
Flux-teknologi
Under fremstillingsprocessen gennemgår fluxbasen (batch) adskillige behandlingsprocedurer, herunder smeltning, granulering, støbning og kvalitetskontrol. Råmaterialet til ladningen før produktionsprocessen er opdelt i små, mellemstore og store. Hver batch gennemgår en grundig vask og tørring, da renheden og nøjagtigheden i parametrene for den fremtidige flux opretholdes fra begyndelsen. Derefter udføres vejning, dosering og blanding med andre teknologiske komponenter. Smeltning og granulering af flux til svejsning udføres på specialudstyr - gasflamme- eller lysbueovne, pools til at hælde koldt vand og metalpaller bruges. På de sidste stadier af forarbejdningen udføres tørring med sigtning. Flusmiddel, der har bestået inspektion, er pakket i specielle poser eller kasser med ildfaste egenskaber.
GOST-krav til flux
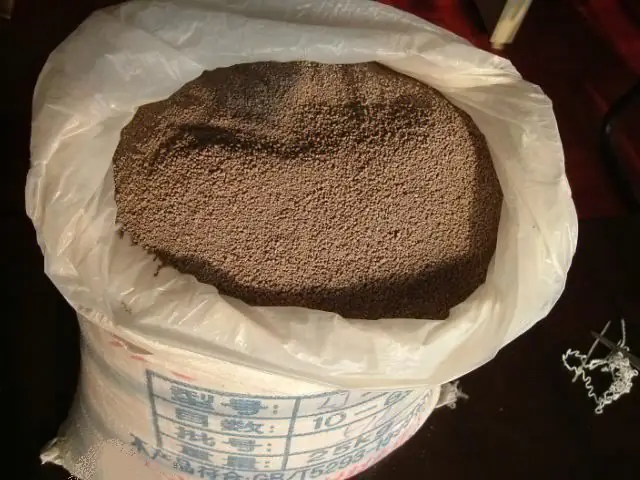
Lovgivningsmæssige krav påvirker flere områder af fluxkvalitetsvurdering, samt regulerer sikkerhedsreglerne for håndtering af materialet og metoder til at teste det. Med hensyn til hovedparametrene stilles følgende krav til dem:
- Udelukket i fluspulverkorn større end 1,6 mm. Procentdelen af deres indhold bør ikke være mere end 3 % af den samlede masse.
- Det er tilladt at producere en flux med en brøkdel på op til 0,25 mm, hvis denne betingelse oprindeligt var aft alt med forbrugeren.
- Det er også efter aftale med forbrugeren tilladt at fremstille materiale med en kornfraktion fra 0,35 til 2,8 mm, men kun i forhold til AN-348-A-kvaliteten.
- Fugtindholdet i flusmidler, afhængigt af mærket, bør ikke overstige en koefficient fra 0,05 til 0,1%.
Hvad angår sikkerhedskrav, er personlige beskyttelsesforanst altninger hovedemnet i GOST-reguleringen. Dykbuesvejsning skal udføres i overensstemmelse med brandsikkerhedsforanst altninger. Separat bør koncentrationen af det anvendte fluspulver, som som standard anses for at være kemisk farligt og skadeligt for produktionen, kontrolleres.
Fuseret og ikke-smeltet flux
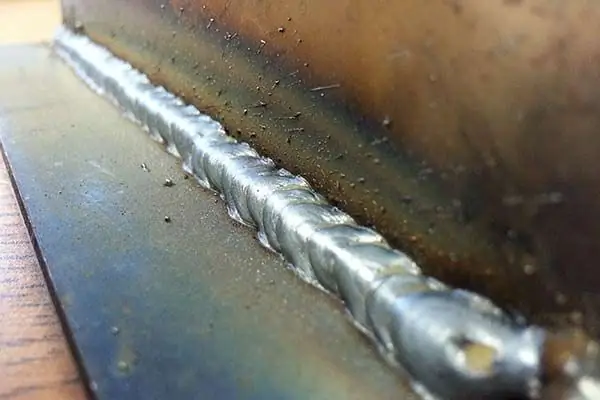
Indholdet af smeltet pulver dannes hovedsageligt af slaggedannende komponenter. De er fremstillet som et resultat af sammensmeltningen af bestanddele, herunder kvartssand, manganmalm og kridt. Ved at blande dem i bestemte proportioner, efterfulgt af smeltning i ovne, er det muligt atfå en modifikator til en søm med et bestemt sæt egenskaber. Mere funktionel er dykket lysbuesvejsning produceret på en usmeltet måde. Dette er en blanding af granulerede og pulveriserede materialer, som ud over den slaggedannende base også indeholder legeringselementer og deoxidationsmidler. Fraværet af en smelteoperation gør det muligt at indføre metalstøv og ferrolegeringer i fluxen, hvilket vil dechifrere mulighederne for at forbedre samlinger.
Typer af nedsænket buesvejsning
Med brug af flusmiddel kan både manuel og automatisk svejsning udføres - den grundlæggende forskel vil afhænge af det valgte udstyr. Buesvejsning udføres i selvjusterende tilstand eller understøttet af automatisk spændingskontrol. Det er optim alt at anvende inverterinstallationer, suppleret med trådfremføringstromler. Svejsning med flux uden gas er også almindelig, som som standard fungerer som et beskyttende miljø mod ilt og nitrogen. Hvad er den gode teknik, der udelukker denne barriere for negative påvirkningsfaktorer? For det første, hvis en passende flux er valgt, vil den være i stand til at udføre hele listen over beskyttende og hjælpeopgaver i forhold til den dannede søm. For det andet letter fraværet af et gasformigt medium selve organiseringen af processen. Det er ikke nødvendigt at forberede en cylinder med en argon-kuldioxid-blanding, og også beskytte svejseområdet mod overdreven termisk eksponering, når du bruger en brænder.
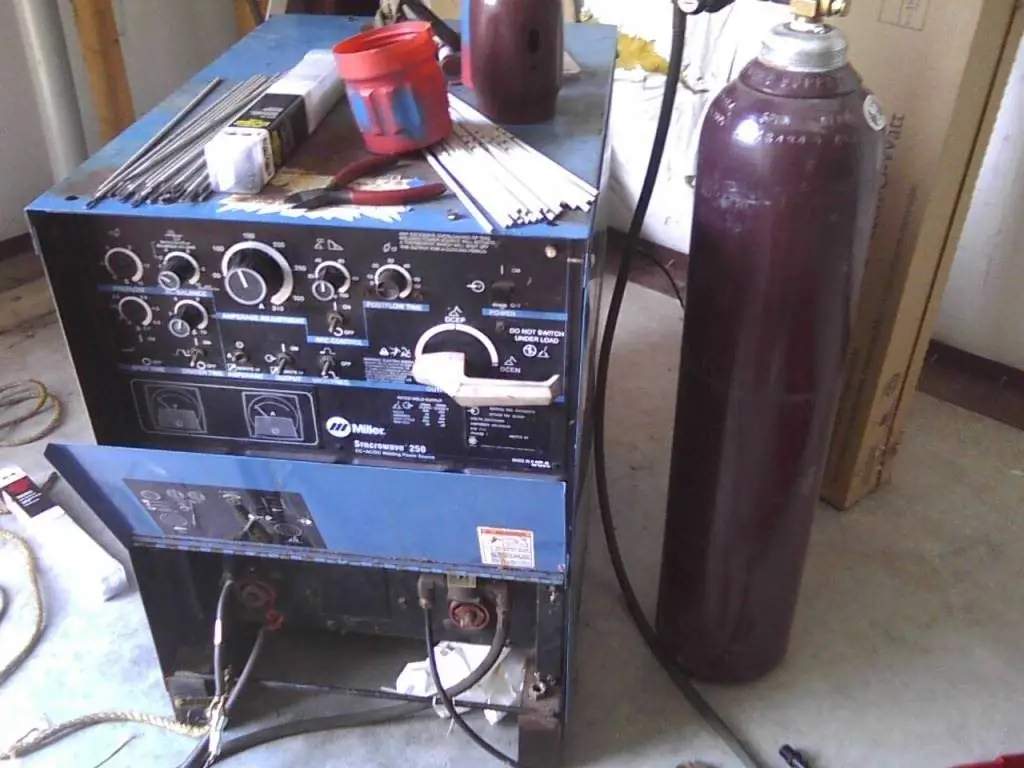
Fluxteknik
Efter tænding af lysbuen skal operatøren vedligeholde denmellem enden af elektroden og emnet under fluxlaget. Pulveret hældes i et lag på 55-60 mm, hvorefter buen bogstaveligt t alt skal druknes i denne masse, indtil den smelter. Med en gennemsnitlig fluxvægt kan dets statiske tryk på metallet være omkring 8-9 g / cm2. Denne værdi er tilstrækkelig til at eliminere uønskede mekaniske effekter på svejsebadet. Ved brug af en tråd til svejsning med flux er det muligt at opnå minim alt smeltesprøjt. Denne betingelse er opfyldt ved at sikre stabil kontakt af smeltezonen med forbrugstråden og fluxen, samt ved at regulere strømstyrken. Beskyttelse fra gassiden er heller ikke påkrævet i dette tilfælde, men strømstyring vil være særlig vigtig. Som regel bruges en kombination af tråd og flux ved svejsning ved en høj strømtæthed, derfor skal maskinen vælges under hensyntagen til opretholdelsen af en konstant hastighed for styring af elektrodegevindet.
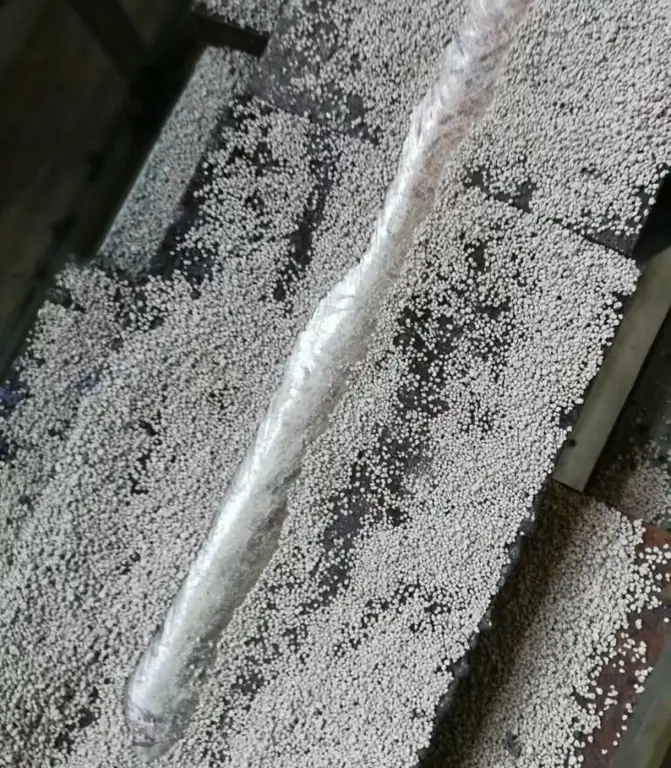
Fordele ved at bruge flux
Brugen af flux påvirker bestemt dannelsen af sømmen på den bedste måde, da de negative faktorer ved arbejdsprocessen under friluftsforhold minimeres. De åbenlyse fordele omfatter reducerede defekter i ledområdet, minimering af sprøjt og mere effektiv lysbuekontrol med fuld autokontrol. Hvad der også er meget vigtigt, er det neddykkede buesvejseområde altid synligt for operatøren. Dette giver mulighed for, om nødvendigt, at foretage rettidige justeringer af processen, og i nogle tilfælde endda undvære særligemasker.
Ulemper ved at bruge flux
Svagheder ved denne teknologi er forårsaget af højere krav til udstyr, da der kræves mere strøm for effektivt at smelte fluxen. I dag produceres specielle modifikationer af enheder til argonbuesvejsning i et fluxmiljø, som har specielt udstyr til dets forberedelse og levering. Det er logisk, at sådanne modeller koster 15-20% mere. En anden ulempe er forbundet med en stigning i smeltezonen. Selvom det kan kontrolleres inden for visse grænser, er det problematisk at behandle små elementer under sådanne forhold.
Konklusion
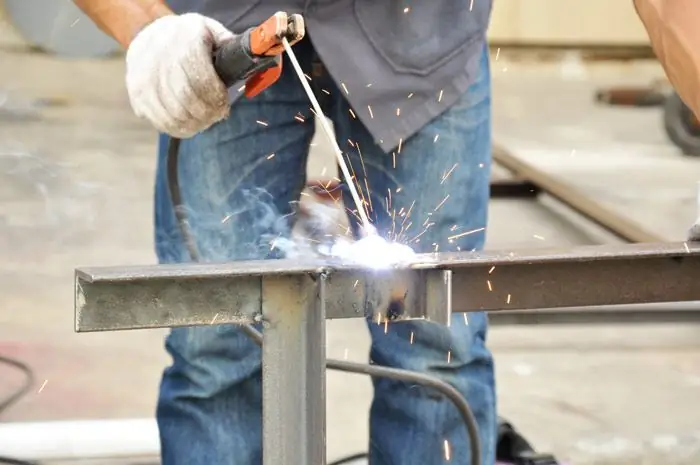
Flux som et forbrugsstof, der forbedrer kvaliteten af svejseprocessen, letter mange produktions- og konstruktionsaktiviteter af dette spektrum. Men selv derhjemme bruges det ofte i landet, i garagen eller blot i reparationsoperationer. Når du vælger dette materiale til dine egne behov, er det meget vigtigt ikke at fejlberegne kvalitetsvurderingen. Som bemærket af samme GOST skal flux til svejsning leveres til markedet i tykke papirposer fra 20 til 50 kg, hvilket indikerer transportmærker. Ved særlig bestilling kan der også laves småemballage, men der skal sørges for særlige beholdere hertil. Desuden bør vejningen udføres med en maksimal fejl på 1 % i forhold til den samlede taravægt.
Anbefalede:
Indikatorer uden forsinkelse og gentegning: typer, funktionsprincip, fordele og ulemper ved anvendelse, ekspertrådgivning
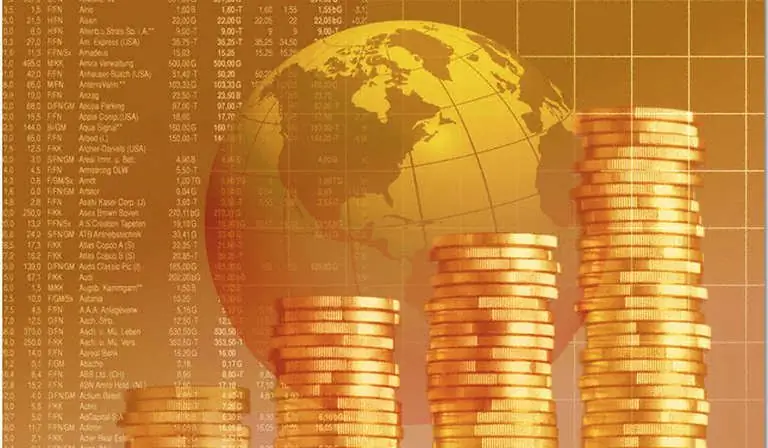
Der er en lang række forskellige værktøjer inden for handel: grafiske konstruktioner, tekniske indikatorer, automatiserede programmer, handelssignaler og meget mere. For at kunne anvende dem i handel, skal du forstå, hvordan de fungerer. Indikatorer uden forsinkelse og gentegning er især populære blandt handlende
Forbindelser: formål, typer af forbindelser. Eksempler, fordele, ulemper ved typer af forbindelser
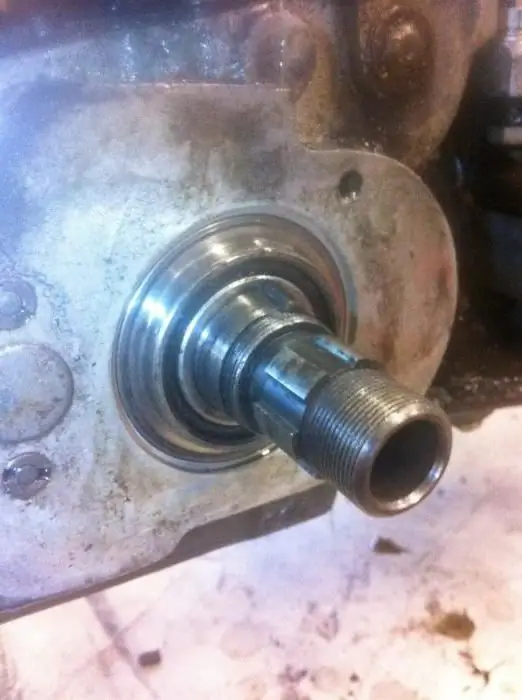
Maskiner og værktøjsmaskiner, udstyr og husholdningsapparater - alle disse mekanismer har mange detaljer i deres design. Deres forbindelse af høj kvalitet er en garanti for pålidelighed og sikkerhed under arbejdet. Hvilke typer forbindelser er der? Lad os se nærmere på deres egenskaber, fordele og ulemper
Mineralulds massefylde: klassificering, fordele og ulemper, formål med mineraluld og anvendelse
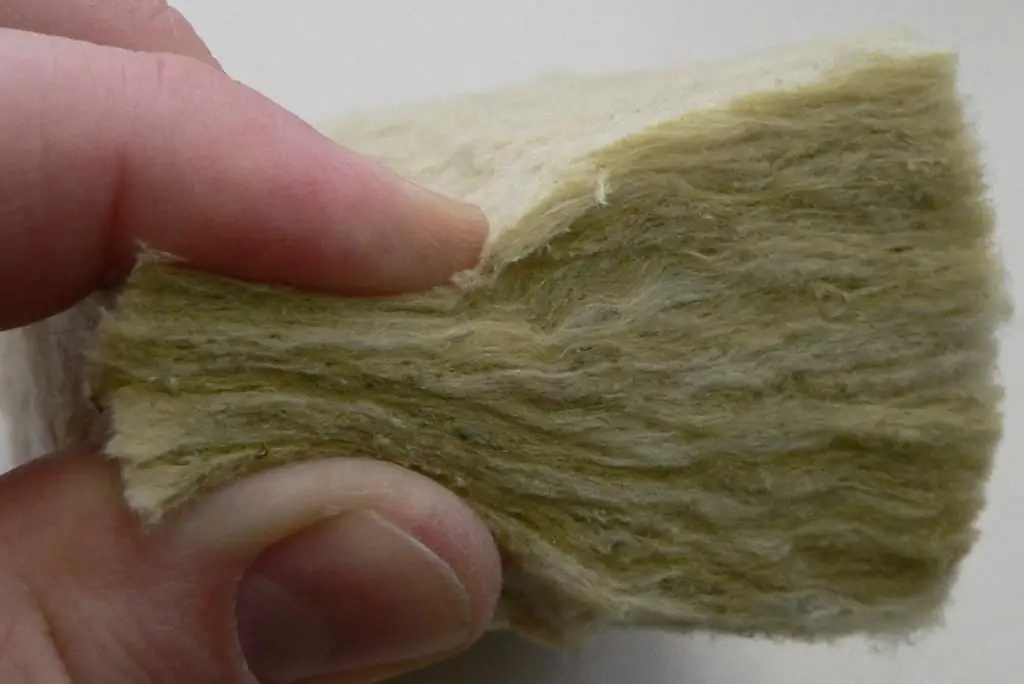
Mineraluld er den mest populære type isolering til en lejlighed eller et hus. I dag bruges den af alle, lige fra bygherrer til ejeren af lejligheden, der ønskede at isolere rummet. Enkelheden af dens installation giver dig mulighed for straks at isolere hele huset (loft, vægge, gulv). Vi vil studere funktionerne og egenskaberne ved det navngivne materiale længere i artiklen
Modstående blok: typer, klassificering, karakteristika, valgtips, fordele og ulemper ved anvendelse
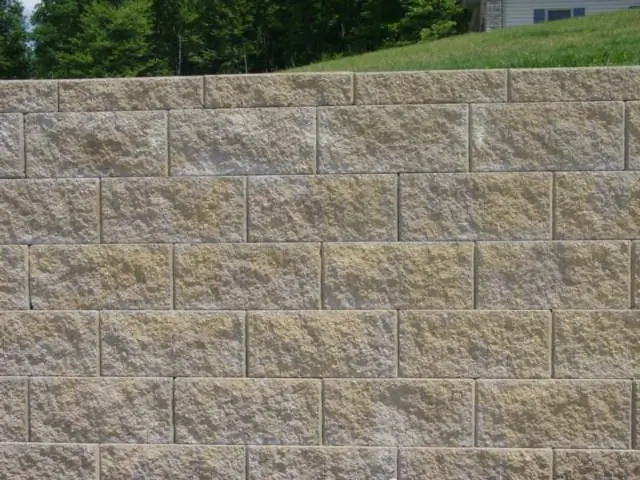
I dag er der mange forskellige materialer til byggeri. Facing blok er en af dem. Det er for nylig blevet brugt ret ofte på grund af dets unikke egenskaber. Det er værd at bemærke, at dette materiale giver dig mulighed for at spare en betydelig mængde materielle ressourcer
Glidelejer: design, typer, produktion, formål, fordele og ulemper
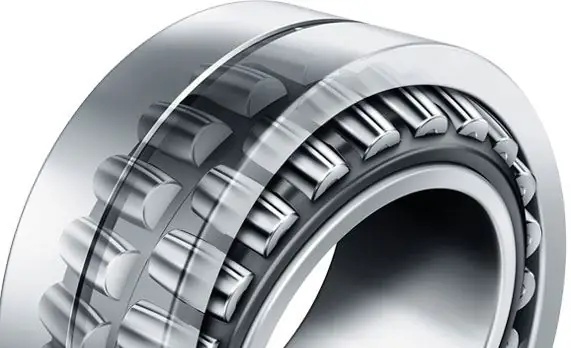
Glidende lejer bruges i generatorer og forbrændingsmotorer. Disse er dele, der er i stand til at overføre drejningsmoment, hvilket sikrer normal drift af mekanismer. Lejer har et specifikt design. Dette giver et bestemt sæt tekniske og operationelle egenskaber for delen. Designegenskaberne ved glidelejer, deres varianter, fordele og ulemper vil blive diskuteret i artiklen