2024 Forfatter: Howard Calhoun | [email protected]. Sidst ændret: 2023-12-17 10:22
Lederen af enhver virksomhed, uanset aktivitetsområde, drømmer om, at overskuddet vokser, og produktionsomkostningerne forbliver uændrede. "5S"-systemet i produktion (i den engelske version 5S), som kun er baseret på rationel brug af interne reserver, hjælper med at opnå dette resultat.
Dette system blev ikke oprettet fra bunden. Noget lignende i slutningen af det 19. århundrede blev foreslået af amerikaneren Frederick Taylor. I Rusland blev dette gjort af videnskabsmanden, revolutionæren, filosoffen og ideologen A. A. Bogdanov, som udgav en bog om principperne for videnskabelig ledelse i 1911. På grundlag af bestemmelserne deri indførte USSR NOT, det vil sige den videnskabelige organisation af arbejdet. Men det mest perfekte var 5C-systemet foreslået af den japanske ingeniør Taiichi Ohno og introduceret af ham på Toyota Motor-fabrikken i produktion. Hvad er det, og hvorfor er det japanske system blevet så populært?
Faktum er, at det er baseret på et simpelt princip, der ikke kræver omkostninger. Den består iden næste - hver medarbejder, fra rengøringsassistenten til direktøren, bør optimere sin del i den overordnede arbejdsgang så meget som muligt. Dette fører til en stigning i overskuddet af produktionen som helhed og til en stigning i indkomsten for alle dens ansatte. Nu er stafetten for indførelsen af "5C"-systemet blevet samlet op af virksomheder over hele verden, inklusive Rusland. I denne artikel vil vi forsøge at overbevise skeptikere om, at japansk knowhow virkelig fungerer, og i absolut ethvert aktivitetsområde.
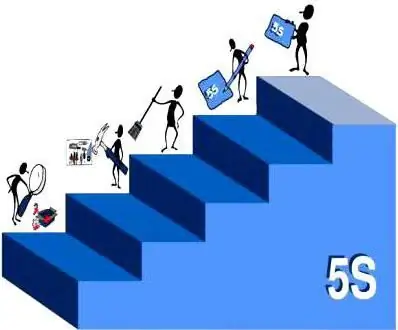
"5C"-systemet i produktion, hvad er det
International 5S står for fem trin ("trin" på engelsk trin). Nogle økonomer og fortalere for en ny holdning til arbejde forklarer navnet med de fem japanske postulater, der konsekvent er implementeret i 5S-systemet: seiri, seiton, seiso, seiketsu og shitsuke. For os er vores indfødte "5C'er" tættere og mere forståelige - fem på hinanden følgende trin, der skal gennemføres for at opnå velstanden i vores produktion. Dette er:
1. Sorter.
2. Holder orden.
3. Holder rent.
4. Standardisering.
5. Forbedring.
Som du kan se, kræver "5C"-systemet ikke noget overnaturligt i produktionen. Måske er det derfor, man stadig kan møde mistillid og en useriøs holdning til hende.
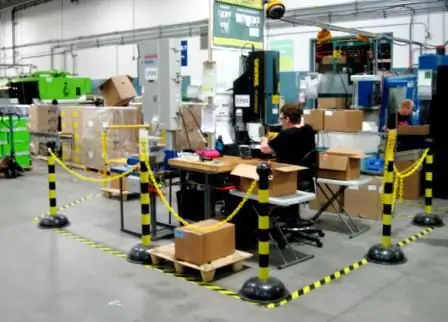
stadier af oprettelse af et system
Den kloge japaner Taiichi Ohno, som takket være introduktionen af sine metoder på Toyota-fabrikken formåede at rejse sig fraingeniør til CEO, bemærket, hvor mange tab der opstår på grund af forskellige uoverensstemmelser og overlejringer. For eksempel blev der ikke sat nogle små skruer på transportbåndet i tide, og som følge heraf stoppede hele produktionen. Eller omvendt, delene blev leveret med en margin, de viste sig at være overflødige, og som følge heraf måtte en af medarbejderne tage dem med tilbage til lageret, hvilket betyder, at de spilder deres tid på tomt arbejde. Taiichi Ohno udviklede et koncept, han kaldte "just in time". Det vil sige, at præcis så mange dele som nødvendigt nu blev leveret til transportøren.
Andre eksempler kunne gives. "5S"-systemet i produktion omfattede også begrebet "kanban", som på japansk betyder "reklameskilt". Taiichi Ohno foreslog at sætte et såkaldt "kanban"-mærke på hver del eller hvert værktøj, hvori alle nødvendige oplysninger om delen eller værktøjet blev givet. Dybest set gælder det alt. For eksempel til varer, medicin, mapper på kontoret. Det tredje koncept, som 5S-systemet i produktionen er baseret på, er konceptet "kaizen", som betyder løbende forbedringer. Der blev også udtænkt andre koncepter, som kun var egnede til højt specialiserede produktionsprocesser. I denne artikel vil vi ikke overveje dem. Som et resultat af alle de innovationer, der er testet i praksis, er der dannet 5 trin, der er anvendelige til enhver produktion. Lad os analysere dem i detaljer.
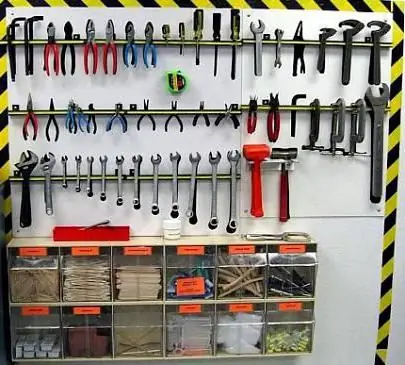
Sortering
Mange af os har varer på vores stationære computere, som istort set ikke nødvendigt. For eksempel gamle formularer, ubrugte filer, udkast til beregninger, en serviet, hvorpå der var en kop kaffe. Og blandt dette kaos kan der være de nødvendige filer eller dokumenter. Grundprincipperne i "5S"-systemet går ud på at optimere din arbejdsgang, det vil sige at sikre dig, at tiden ikke spildes på at lede efter de rigtige ting blandt murbrokkerne af det unødvendige. Det her er sortering. Det vil sige, på arbejdspladsen (nær maskinen, på bordet, på værkstedet - hvor som helst) er alle genstande lagt ud i to bunker - det nødvendige og det unødvendige, som skal bortskaffes. Yderligere er alt, hvad du har brug for, opdelt i følgende bunker: "bruges ofte og konstant", "bruges sjældent", "næsten ikke brugt". Dette afslutter sorteringen.
Keeping order
Hvis du bare skiller genstandene ad, er der ingen mening. Det er nødvendigt at arrangere disse genstande (værktøjer, dokumenter) i en sådan rækkefølge, at det, der bruges konstant og ofte, er i syne, eller så det hurtigt kan tages og nemt lægges tilbage. Det, der sjældent bruges, kan sendes et sted i en æske, men der skal påsættes et kanban-tag, så det efter et stykke tid nemt og præcist kan findes. Som du kan se, starter 5S-systemet på arbejdspladsen med de enkleste trin, men faktisk viser det sig at være meget effektivt. Og desuden forbedrer det humøret og lysten til at arbejde.
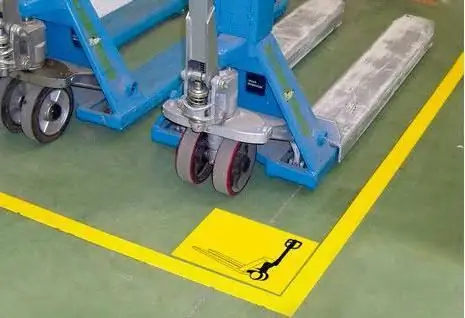
Keeping clean
Dette tredje trin er det mest logiske for mange. Vi har lært at være rene fra barndommen. På deni produktionen er det også nødvendigt, og ikke kun kontorarbejdernes borde eller skabe i cateringvirksomheder, men også maskiner, bryggers til rengøringsmidler skal være rene. I Japan passer medarbejderne godt på deres arbejdspladser, de bliver gjort rent tre gange om dagen - om morgenen før arbejde, ved frokosttid og om aftenen, sidst på arbejdsdagen. Derudover har deres virksomheder indført speciel mærkning af områder, der giver dem mulighed for at observere orden i produktionen, dvs. områder med færdige produkter, opbevaring af visse dele og så videre er markeret med forskellige farver.
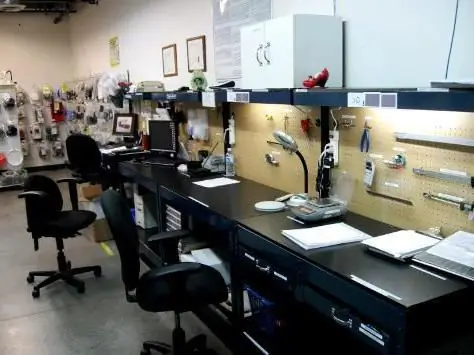
Standardisering
Standardiseringsprincipperne blev opfundet af Taiichi Ohno. De er også meget brugt af det moderne 5S-system. Produktionsstyring, takket være standardisering, får et vidunderligt værktøj til at kontrollere alle processer. Som et resultat elimineres årsagerne til forsinkelser fra tidsplanen hurtigt, og fejl, der fører til frigivelse af produkter af lav kvalitet, bliver rettet. På Toyota Motor-fabrikken så standardiseringen således ud: værkførere udarbejdede daglige arbejdsplaner, præcise instruktioner blev slået op på arbejdspladsen, og ved arbejdsdagens afslutning kontrollerede specialarbejdere, hvilke afvigelser fra planen, der skete i løbet af dagen og hvorfor. Dette er den grundlæggende regel for standardisering, det vil sige præcise instruktioner, arbejdsplaner og kontrol over deres implementering. Nu indfører mange virksomheder, for eksempel ENSTO-fabrikker i Estland, et bonussystem for medarbejdere, der nøje overholder bestemmelserne i 5C-systemet og på baggrund heraf øger deres produktivitet, hvilketer et stort incitament til at adoptere dette system som en livsstil.
Forbedring
Det femte trin, som fuldender "5S"-systemet i produktion, er baseret på konceptet kaizen. Det betyder, at alle medarbejdere, uanset deres stilling, bør stræbe efter at forbedre arbejdsprocessen på det område, de har fået betroet. Den filosofiske essens af kaizen er, at hele vores liv bliver bedre hver dag, og da arbejde er en del af livet, bør det heller ikke holde sig væk fra forbedringer.
Aktivitetsfeltet her er bredt, for perfektion har ingen grænser. Ifølge japanernes koncepter skulle arbejderne selv ønske at forbedre deres produktionsproces, uden instruktioner eller tvang. Nu er mange organisationer ved at opbygge teams af medarbejdere, der overvåger produktkvalitet, lærer andre om deres positive oplevelse og hjælper med at opnå ekspertise.
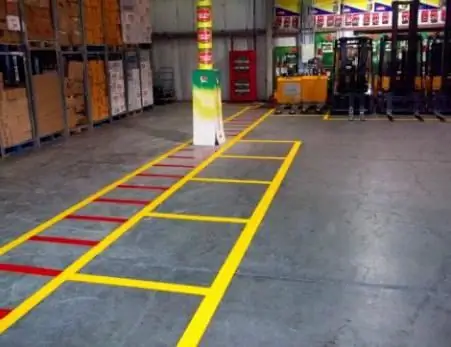
Grundlæggende fejl
For at "5C"-systemet kan begynde at virke, er det ikke nok at organisere det eller ansætte medarbejdere, der vil tvinge deres kolleger til at implementere det. Det er vigtigt, at folk indser nytten af denne innovation og accepterer den som en livsstil. Indførelsen af "5S"-systemet i Rusland i produktionen står over for vanskeligheder, netop fordi vores russiske mentalitet er anderledes end den japanske. Mange af vores produktioner er kendetegnet ved følgende:
1. Medarbejdere, især hvis der ikke er incitamenter for dem, søger ikke at øge virksomhedens overskud. De spørger,hvorfor prøve at gøre chefen endnu rigere, hvis han allerede har alt.
2. Lederne selv er ikke interesserede i indførelsen af "5S"-systemet, fordi de ikke ser det hensigtsmæssige i det.
3. Mange direktiver "ned fra oven" er vant til kun at udføre for "tick". I Japan er der en helt anden holdning til deres arbejde. For eksempel tænkte den samme Taiichi Ohno, der introducerede "5S"-systemet, ikke på personlig vinding, men på fordelene ved det firma, hvor han kun var ingeniør.
4. På mange virksomheder bliver 5S-systemet tvangsintroduceret. Lean produktion, som indebærer eliminering af tab af enhver art (arbejdstid, råvarer, gode medarbejdere, motivation og andre indikatorer), virker ikke, da arbejdere begynder at modstå innovationer på et underbevidst niveau, hvilket i sidste ende reducerer alle anstrengelser til nul.
5. Ledere, der implementerer systemet, forstår ikke fuldt ud dets essens, hvilket forårsager fejl i etablerede produktionsprocesser.
6. Standardisering udvikler sig ofte til bureaukrati, en god gerning er overgroet med instruktioner og direktiver, der kun forstyrrer arbejdet.
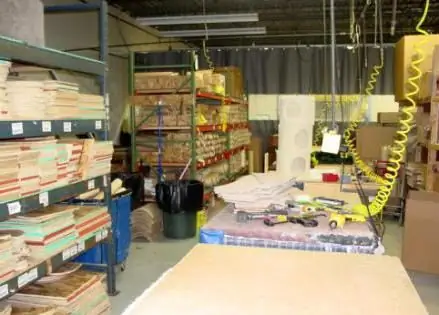
Anmeldelser
Russere, der har introduceret "5S"-systemet i produktionen, feedbacken på denne innovation er meget tvetydig. Fremhævede fordele:
- bedre at være på arbejdspladsen;
- ditraher ikke fra arbejdet med unødvendige småting;
- mere klar arbejdsgang;
- trætheden aftog i slutningen af skiftet;
- en smule øgetløn ved at øge arbejdsproduktiviteten;
- arbejdsskader faldt.
Noterede ulemper:
- når de sorterer, tvinger de alt til at blive smidt ud;
- standardisering har ført til øget bureaukrati;
- Introduktionen af "5C"-systemet har ikke forværret problemerne på alle områder af virksomheden;
- At sætte 5S-systemet på førstepladsen har overskygget vigtige problemer såsom manglen på reservedele.
Anbefalede:
Porters strategier: grundlæggende strategier, grundlæggende principper, funktioner
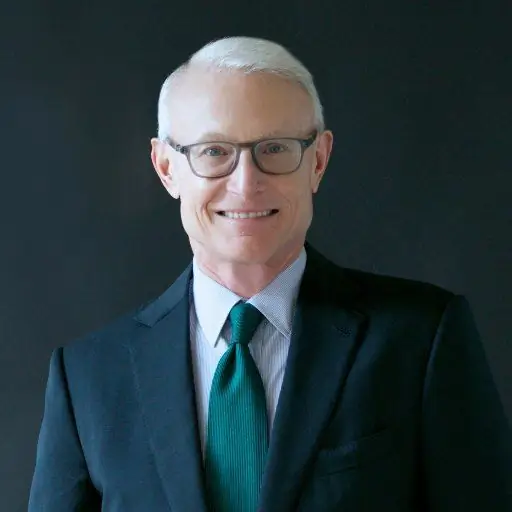
Michael Porter er en anerkendt økonom, konsulent, forsker, lærer, foredragsholder og forfatter til adskillige bøger. som udviklede deres egne konkurrencestrategier. De tager højde for markedets størrelse og træk ved konkurrencefordele. Disse strategier er detaljeret beskrevet i artiklen
Mystery shopper: hvad er det, funktioner og principper for erhvervet
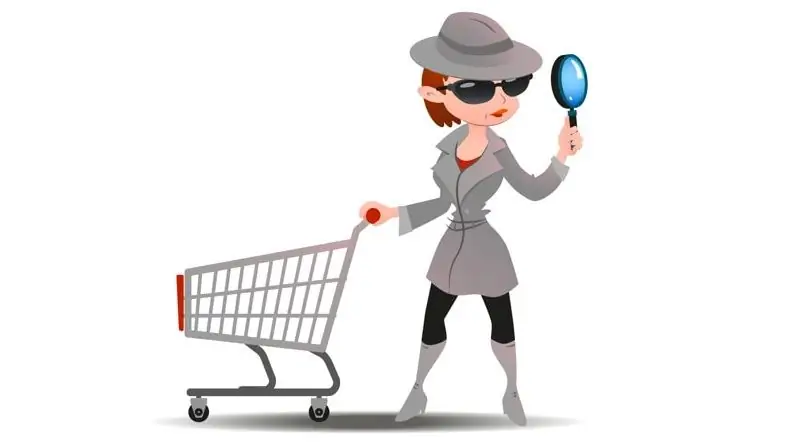
"Mystery Shopper"-metoden er meget brugt i vestlige virksomheder, men er for nylig blevet kendt på det russiske marked. Overvej hvilken slags erhverv det er, hvor man skal søge ledige stillinger, hvilke kvaliteter en ansøger til stedet for en mystery shopper skal opfylde, og også hvordan kvaliteten af arbejdet vurderes og mulige fejl
Grundlæggende principper for udlån: beskrivelse, funktioner og krav
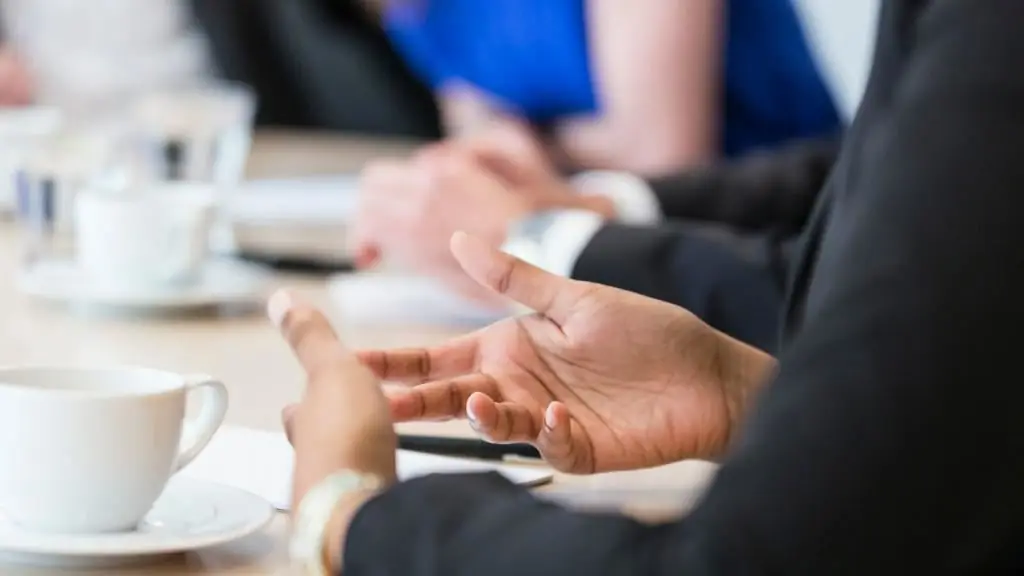
I vores svære tid er folk ofte plaget af økonomiske problemer. En af de bedste løsninger i denne situation er et lån. Find ud af, hvad principperne for udlån er, og om du opfylder kriterierne for en eksemplarisk låntager
Moderne produktion. Strukturen af moderne produktion. Problemer med moderne produktion

Udviklet industri og et højt niveau af landets økonomi er nøglefaktorer, der påvirker befolkningens rigdom og velfærd. En sådan stat har store økonomiske muligheder og potentiale. En væsentlig del af økonomien i mange lande er produktionen
JSC "Yaroslavl Tire Plant": beskrivelse, produkter, produktion og anmeldelser
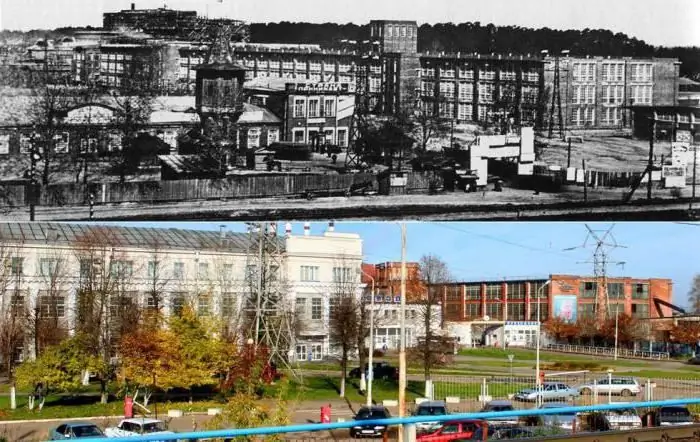
JSC Yaroslavl Tire Plant uden overdrivelse er lederen af landets dækindustri. Hvert år producerer virksomheden omkring 3 millioner enheder af højkvalitetsprodukter til forskellige typer udstyr. Selskabet er en del af bedriften "Cordiant"